Now that most of the major chassis work is done, there has been a bit of a “phase shift” in working on my car and it’s taken me a bit of time to get used to. In short, I got a little spoiled with the “visual” reward I got when making large panel replacement progress because it simply looked like I was making big progress. In the past few weeks, I have accomplished a lot of small things that add up, but I found myself struggling with feeling like I was underachieving on all these smaller jobs because the visual impact just wasn’t what I was used to after the past two years. But, as I have conditioned myself to do, I put my head down and kept moving and pretty soon………more progress. I like that!
When I last left off, I had to complete the front trunk floor seam by fully welding it along the bottom of the car and grinding all that work smooth for priming a filling later on. In addition, I added the front corner reinforcements and the rear bumper brackets to round out the repairs at the back of the car. Fortunately, all of this work was quite uneventful as everything had pretty much been nailed down in the earlier work such that this remaining work practically fell into place. As a final test (and a bit of personal entertainment), I test fit the upper coilover mount in place and was happy to see it lined up perfectly and will do a good job hiding any sign of the weld seem in the axle tunnel area that may try to give itself away.
My next short project was to make some small repairs to my axle housing, tidy up the 9-inch differential housing and get the new Moser 31-spline axles ready for battle.
Quite some time ago, I identified some small cracks at the spring perch welds on the axle housing no doubt caused by past abuse. After cutting of the spring perches in preparation for the installation of the Heidts 4-link brackets, the time was right to weld up these flaws along with filling a few weld gouges left behind so that the axle tubes would be in good shape for the new brackets. With these repairs out of the way, I can now concentrate on getting the 4-link brackets mocked up, welded and finished in time for the weather here to warm up enough to allow me to sand blast the completed housing in preparation for powder coating.
Once I had the housing in shape, I shifted focus to the 9-inch differential case restoration. In the past few months I spent a good bit of time “decoding” the differential in my car. While I knew the housing was original, I also knew the differential case was not. Originally, my car came with a 4.30 Detroit Locker diff, however when I purchased the car, the diff it came with was a measly 3.50 open 31-spline crapper. As luck would have it, the housing itself was the genuine article: A nodular iron case with a rare Daytona pinion support intact and in fantastic condition.
Confident that I was working with something worthy, I stripped the differential completely and deburred everything to remove all of the clag and sharp edges. I soaked the parts in Purple Power liquid cleaner to remove all traces of the original red oxide coating on the unit and ran it through the blast cabinet to clean the more stubborn soil off the parts. Then, everything spent a few days soaking in a nice, fresh chelant bath using Esprit Performance’s new chelant offering that does not include metal cleaners. As I have become so accustomed to over the past year, this stuff kicks major butt! Every piece of the differential (and a lot more pieces I will report on at a later time) came out perfectly free of rust with absolutely no elbow grease. The part condition was so good in fact, that I simply dried the parts off and went straight to powder coating with no hassles whatsoever.
After I had applied a fresh coating of satin black urethane powder on all of the diff pieces, I shifted focus to the interior surfaces. To coat and protect these surfaces, I turned to a venerable coating know far and wide in performance circles. The product is called Glyptal and is an offshoot of General Electric. The proper name for the paint is #1201 Red Enamel (insulating paint), but its original purpose was an armature paint for industrial electric motors. Over the decades, its uses have expanded considerably, even to include the interiors of many performance and racing engines. I have never condoned painting the interior surfaces of any machine using a pressurized lubrication system, but in cases where the machine is splash oiled, like a differential or perhaps a Model T engine, then Glyptal is a fine candidate. The product does an excellent job sealing the casting to prevent residual core sand and rust from soiling the lube and to provide a nice slippery surface to keep the lube in the sump where it can do its job. A few coats of Glyptal, applied by brush and cured at 250 degrees F for two hours leaves a finish that is surprisingly durable and looks remarkably good.
As I complete this installment, I have my rear Cobra calipers and front pinion support baking in the powder oven with a close eye on the door for Summit Racing to deliver the one lone pinion bearing I need to start putting the restored differential together. Timken roller bearings throughout. Should be as close to bulletproof as I can make it. Also, I plan to mock up the rear axle housing and 4-link suspension in the car to allow me to weld up the rear brackets in place and prep everything for sand blasting and powder. Once that is complete, I will finish assembling the rear axle assembly and put it away until the time comes to put it in there for good.
 |
The lower seam of the forward trunk floor patch was finally welded in. Short stitches of about 1" long were staggered across the seam to minimize warping. |
 |
With the welding complete, I could feel confident that the repair was sturdy and grinding could begin. |
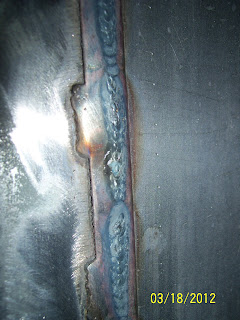 |
Here is a close-up of the top side of the weld seam showing complete penetration of the weld. |
 |
The trunk floor seam from the top. This will all be invisible once the Dynamat material is installed. |
 |
After grinding all of the welds on the bottom of the repair, I was pleased that everything looked like it require little filler to smooth things out. |
 |
I finished the trunk floor repair by adding the corner brackets to duplicate the original feature. |
 |
As a test, I test fit the upper coilover mounting bracket and found that this will work well to hide any imperfections in the joint. |
 |
Bumper bracket alignment was very good right out of the box. This is the left rear bumper bracket after final welding and a pass with the angle grinder to clean things up. |
 |
Here is the left rear bumper bracket from the inside. |
 |
The right rear bumper bracket alignment was also very good straight off. |
 |
Right rear bumper bracket inside view. |
 |
After cutting off the original leaf spring brackets, I found weld gouges and a few small cracks that needed to be repaired before moving on with other modifications. |
 |
Here is a better view of the areas requiring weld repair. |
 |
I dialed up my trusty MIG welder and filled the u-bolt chaffing scars on the housing along with the small cracks and weld gouges. |
 |
A few minutes with the angle grinder and the welds were smoothed up and the evidence of any prior damage was now gone. |
 |
After powder coating the axle bearing retainer plates and installing new wheel studs in the Moser 31-spline axles, I pressed new bearings and lock rings on each axle. |
 |
The finished assembly looks all-business. Note the o-ring seal around the O.D. of the axle bearing. This eliminates the need for axles seals in the housing. |
 |
Decoding my rear differential case revealed a genuine nodular iron unit. |
 |
The interior of the differential was actually in surprisingly good shape. Note the factory red oxide paint on the interior surfaces. |
 |
Another bonus! This is a very desirable but rare "Daytona" pinion support. Other than the casting number, Daytona pinion supports are identified by the very large rear pinion bearings used as opposed to the identically sized (small) bearings used on the front and rear of the pinion in a "standard" 9-inch. |
 |
After stripping the factory paint and scrubbing the red oxide paint off in a bath of Purple Power degreaser, I ran the parts through my blast cabinet and then deburred all the sharp edges with my die grinder. |
 |
Inside the case, I ground down all of the casting flash and sharp edges. |
 |
In preparation for coating, I soaked all of the differential parts in Esprit Performance Rust Remover, my favorite and extremely effective chelation rust remover chemical. Magic stuff. |
 |
Since chelant is 80% water, I cover the tub with a trash bag and a piece of panelling to reduce the evaporation rate. |
 |
With little more prep work than drying the part off straight out of the chelant, I applied my favorite semi-gloss urethane powder coating to the diff case and cured it up. This is a shot straight from the oven and the part is still too hot to touch when I snapped this photo. |
 |
The pinion yoke looks great in fresh powder. |
 |
With the powder work complete, I prepared the inside surfaces of the diff case for a couple of coats of Glyptal #1201. |
 |
Using nothing more than a simple 1" brush, I painted all of the inside surfaces with Glyptal to seal everything up. A second coat was applied a day later. |
 |
Another shot of the fresh Glyptal coating from the pinion nose area. |
 |
Once the Glyptal coating is dry, it's hard to believe it was applied by brush. No brush strokes visible anywhere! |
 |
A look inside the case just before oven curing @ 250 degrees F for two hours. |
 |
Here is the case right from the oven. The Glyptal got a bit darker and slightly more glossy after curing. |
 |
A look inside the pinion nose are and the Glyptal looks great. |
WooHoo - looks of shiny parts!!! Once you go powder - there's no going back! Nice work Sven.
ReplyDeleteBTW, did you powder coat the rear axle housing? And if so, do you have an oven large enough to handle it or did you use one of those IR free standing gizmos?
rj
Yep, I'm in it deep now! LOL
ReplyDeleteI will be coating the axle housing once all of required mods are made for brackets and brake hose mount tabs, etc are complete. Then it's into the oven for the same black urethane powder as the diff case. My powder oven is designed for doing motorcycle and bicycle frames (it's 72 inches high inside), so it will work great for the axle housing. Toughest thing is moving the housing from the booth to the oven because it's so large and bulky.
As they say, Sven, the devil is in the details, and I will say, the details look awesome! The powder coating is sweet. Maybe I'll drop my rear axle housing off at your place on one of my trips to Michigan! LOL! Keep digging. The progress is great.
ReplyDeleteThe one thing I am quickly discovering is the details are expensive! But they sure look good when they're done! And if you ever get up this way, give me a head-up and I'll buy the first round of coffee in exchange for some good Mustang chat!
DeleteHoly cow Sven! Your high quality craftsmanship could give a lot of pro shops a run for their money. That is one sweet-looking diff. Congrats on the rare components and thanks for the intro to Glyptal (for me anyway).
ReplyDeleteThanks very much for that Alex! I have to admit that I enjoy this work so much, the thought has crossed my mind on doing this sort of thing for a living. Always helps to know that what I think looks decent is seen similarly by my fellow enthusiasts. How's your car coming along?
ReplyDelete